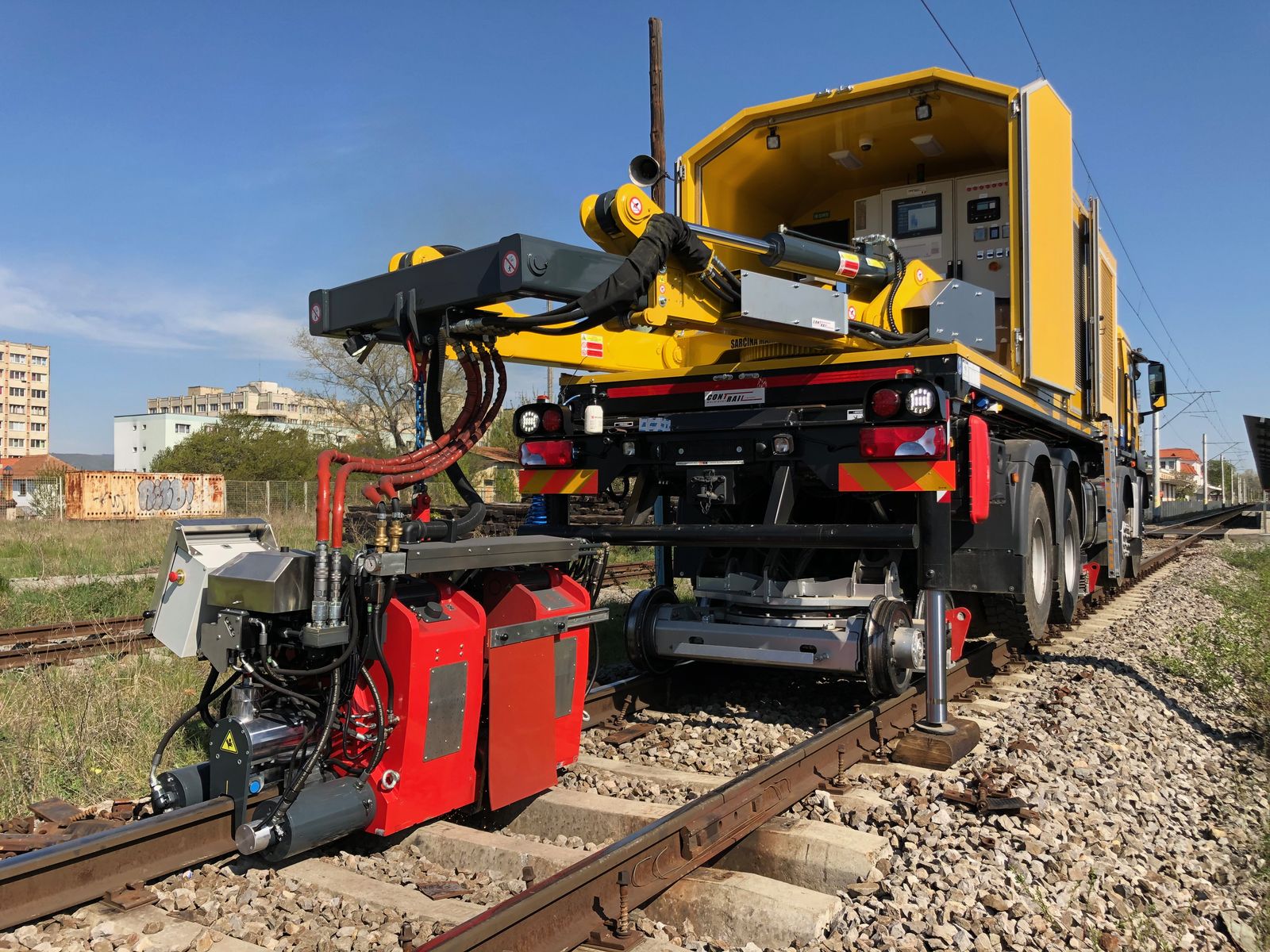
Flash Butt Welding
High-Precision Rail Panel Fabrication
Our flash butt welding plants deliver factory-controlled, high-integrity welded rail panels. Using precision electrical resistance welding, each joint is formed without filler, reducing thermal distortion and improving fatigue resistance.
Patil Group operates India's largest Flash Butt Welding depots, equipped to weld 20-rail panels with advanced infrastructure. With mechanised rail handling systems, these facilities ensure efficiency, safety, and world-class precision for Indian Railways.
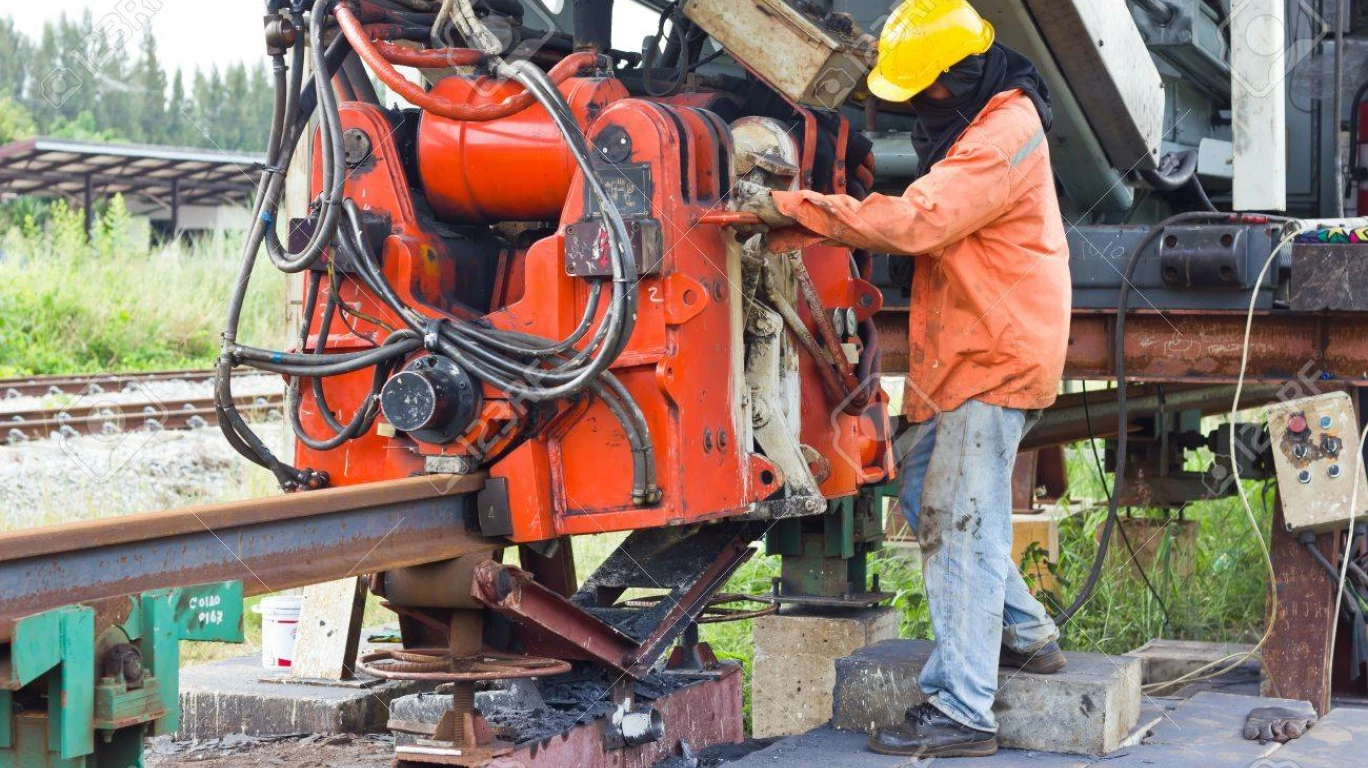
Patil Group's welding plants are located in:
- New Bongaigaon, Assam
- Rangapani, West Bengal
These facilities support large-scale panel production and direct dispatch to project sites.This system has been integral to:
- Northeast Frontier Railway projects
- Konkan Railway sections
- Bridge and tunnel approaches requiring jointless long panels